Solutions
Ultra Low Spatter Welding Technology – Synchro Feed Evolution
Improve productivity and quality with the most advanced robotic wire feeder and heat input system in the industry. This low-spatter technology achieves an ultra-low-spatter weld with no grinding needed.
What is Synchro Feed Evolution?
Synchro Feed Evolution is an ultra low spatter welding technology for robotic MIG, MAG and CO2 welding. The technology developed by OTC DAIHEN, the world’s leader in arc welding technology, combines a revolutionary wire retraction system in the torch with a high-speed processor in the power source that together creates minimal spatter and a stable arc.

Ultra Low Spatter Weld

Reduce Hands-On Time

Reduce Part Setup Time and Fixtures

Replace Manual TIG Welding
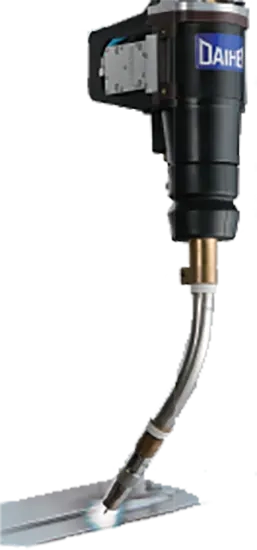
Advancements in Synchro Feed Evolution
The technology has advanced from its initial release as Synchro Feed into Synchro Feed Evolution, which consolidated the torch hardware for faster connection and added two new advanced welding modes for additional capabilities.
Connection Time
Connection time is only 2 minutes with a new coaxial power cable that creates a single connection point.
Push Arc Mode
Weld beads are 30-40% wider and flatter to alleviate issues caused by gaps, poor fit and part deviation.
Pulse Mode
A rippled wave weld is created, ideal for aluminum and thin materials, with precision pulsing between ultra-low spatter and spray transfer modes.
Materials that Benefit from Synchro Feed Evolution
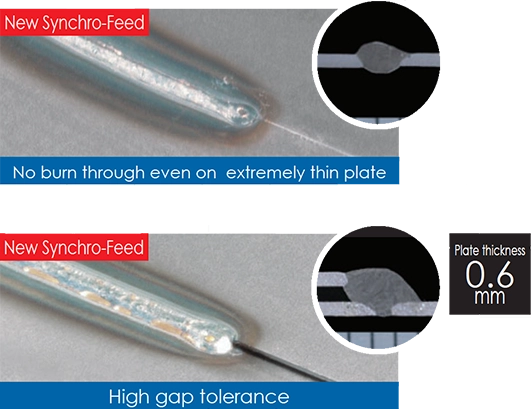
Sheet Metal
High-quality welding and no burn-through on very thin plates, even with 1.2mm wire (helps reduce costs).
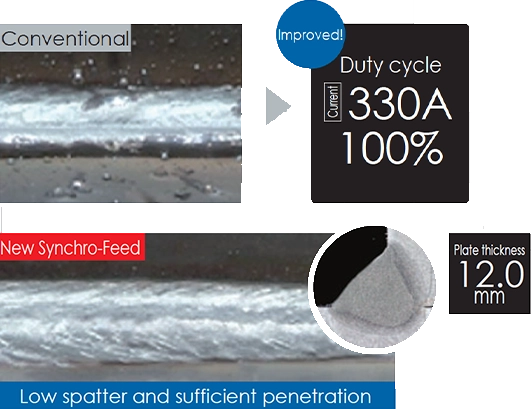
Thick Steel Plate
Low-spatter welding that ensures sufficient penetration even at high current. Torch weaving also achieves a beautiful bead with low spatter.
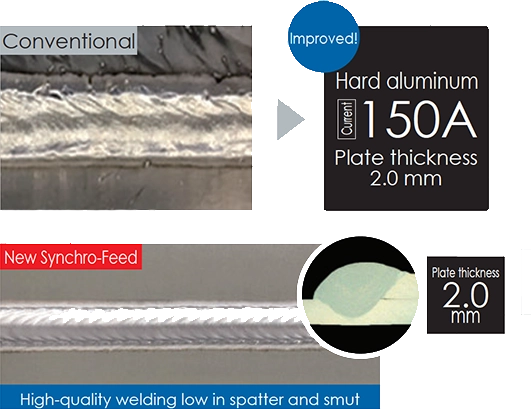
Aluminum
High-quality welding with low spatter achieves low smut with low heat input. Learn more in our article on how the technology is beneficial in welding aluminum and high-tensile steels.

Stainless and Galvanized Steel Plate
High-quality, smooth welding with low spatter, even on stainless and galvanized steel plates. Adaptable to various manufacturing processes.
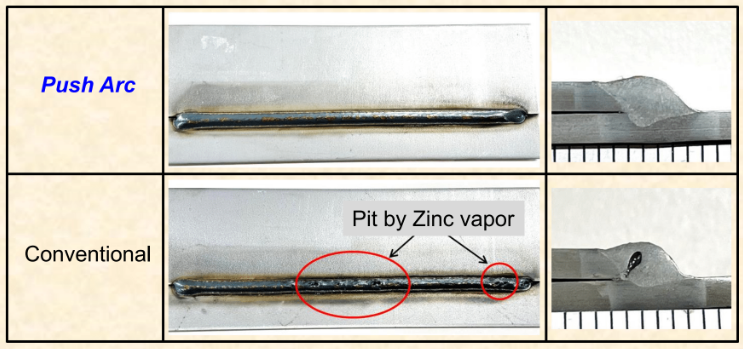
Zinc-Plated Steel
An enlarged molten pool prevents pitting and the formation of blow holes for a higher-quality weld on zinc-plated steel. Learn more in our article on overcoming challenges welding zinc-plated steel.
The Key Components of Synchro Feed Evolution
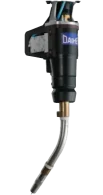
Pull Feeding Unit (Model AFPS-2503 for steel with RT3500H Torch shown)
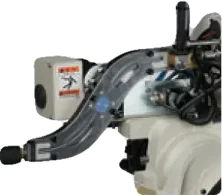
Wire Buffer (Model L-11610 for steel shown)
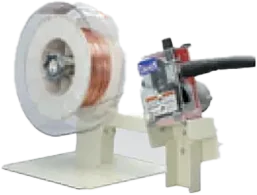
Push Feeder (Model AFS-2301 for steel with Wire Reel Stand shown)
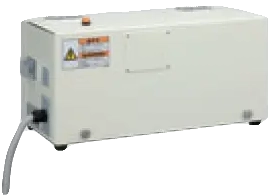
Wire Feed Control Device AFCA-S1W04
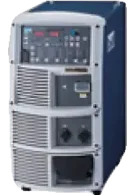
Welding Power Supply WELBEE II P500L
Range of Welding Applications
Range of applications for the Synchro-Feed welding system
Item | Specification | |||||
---|---|---|---|---|---|---|
Material | Mild Steel | Galvanized Steel Plate | Stainless Steel (Ferrite, Austenite) | Aluminum | ||
Shiedling Gas | CO2/MAG | CO2/MAG | MIG (98%Ar+2%O2) | MIG (100%Ar) | ||
Applicable Wire Diameter | ø0.9 | ø1.0 | ø1.2 | ø1.2 | ø1.2 | ø1.2 |
Wire Stock Method | Wire reel/pack wire | |||||
Welding Current | CO2: 50–200A | CO2: 50–250A | CO2: 50–300A | CO2: 50–300A | MIG (98%Ar+2%O2): 50–300A | MIG (100%Ar): 40–150A |
Welding Current | MAG: 50–180A | MAG: 50–250A | MAG: 50–330A | |||
Rated Duty Cycle*1 | 100%*2, *4 | 100%*3, *4 | 100%*2, *4 | 100%*2, *4 | 100%*2, *4 | |
Applicable Tips | Welding Current: 50–200A: FA tip, 200–400A: E tip | Tip for Aluminum | ||||
Max. Cable Length in Conduit | 5m |
*1 Ambient temperature 45°C (113°F)
*2 When used at 100% rated duty cycle, cooling air supplied at 0.30MPa is required.
*3 When CO2 welding at 300A or higher, the RT5000H torch and cooling air supplied at 0.35MPa are required. When MAG welding at 250A or higher, the RT5000H torch and cooling air supplied at 0.45MPa are required.
*4 When no cooling air is supplied, the rated duty cycle is limited to 30%.
Making the Switch from TIG to Robotic MIG
While manual TIG welding can create that precise and aesthetically pleasing weld needed on critical welding tasks, it is time-consuming, difficult to learn and can be a challenge to find skilled labor. Synchro Feed Evolution is proven to create the same welding bead as TIG, allowing for manufacturers to switch from a manual TIG process to a much-faster robotic MIG process.
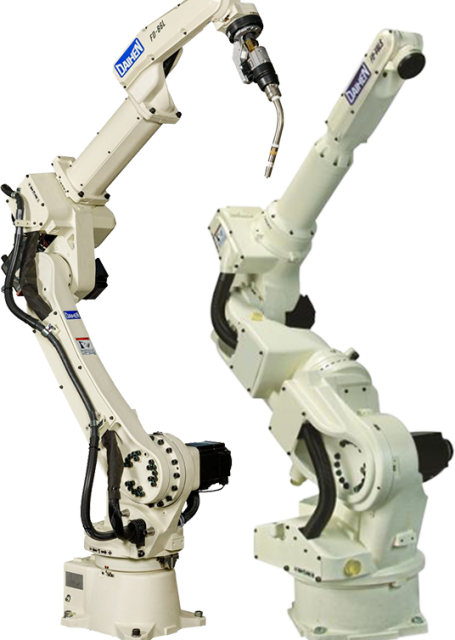
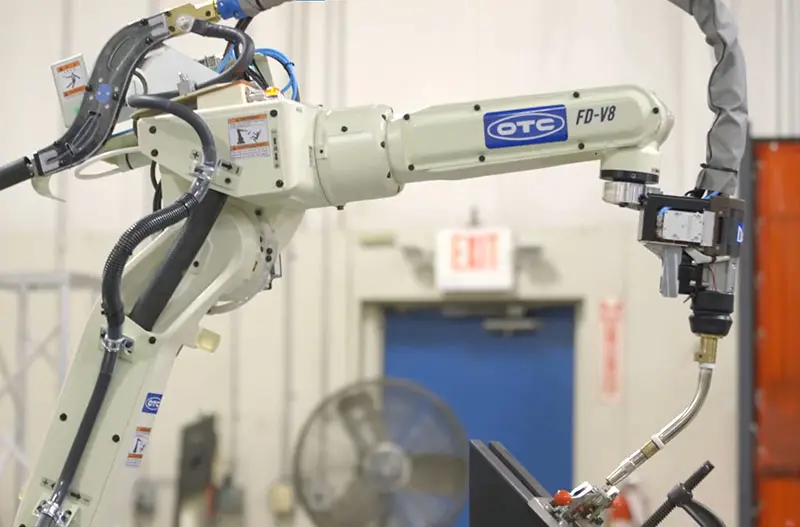
Robotic Welder Training
While there is always a learning curve with new technology, Synchro Feed Evolution and all of OTC DAIHEN’s robotic welding solutions are user-friendly, with on-screen displays of functions, errors and data tracking to help all levels of welders achieve optimal results. OTC DAIHEN also has a Free For Life Training program to ensure your team has the training they need, when they need it.
Why Choose an OTC DAIHEN Arc Welding Robot
- The world’s No. 1 arc welding robot
- A single-source solution with all components manufactured by OTC DAIHEN
- Free training for life
- Expert service and support
6-Axis Robots
7-Axis Robots
Robot Controllers
Robot Positioners
Robot Sensors